When sticky becomes unsticky - the invention of reversible glue
8 January 2024 | By: Newcastle University | 5 min read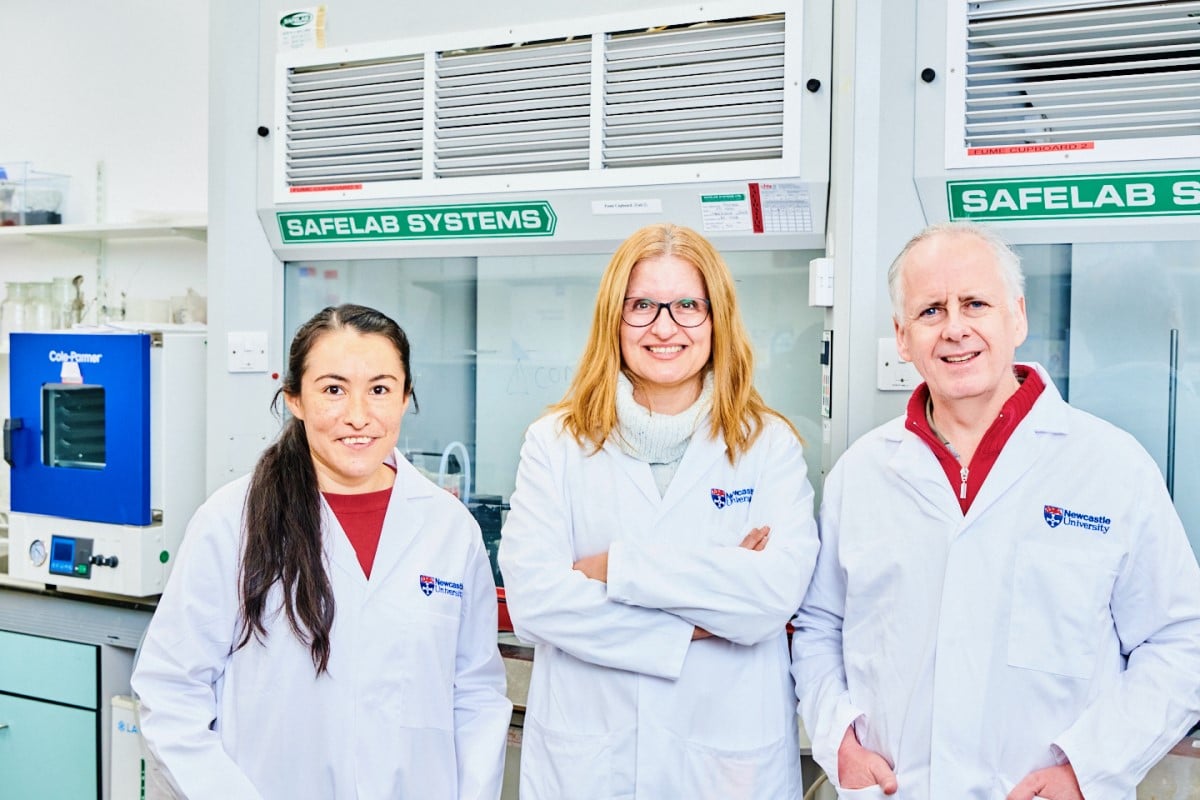
Newcastle University engineers have pioneered a water-based reversible glue that promises to change how we recycle.
With scalability, a long shelf life, stability in humid environments, and versatile material bonding capabilities, this cost-effective adhesive has significant implications for plastics recycling.
In this blog post, the team delves into the transformative potential of the glue, exploring its origins and outlining future plans.
Contents
- What are glues?
- Researching pH-switchable adhesion
- Initiating glue innovation: collaboration, expertise and funding
- Making a reversible glue
- Effective adhesion on challenging surfaces
- Improving industrial processes
- The future: additional funding, extended functionality and team expansion
What are glues?
We have been using glues since the Stone Age. Primitive tools needed primitive handles, which required glues to stick them together. Early adhesives were based on plants, and it is only in the past hundred years that glues were replaced by petroleum-based materials.
Contemporary glues are intrinsically environmentally unfriendly due to the increased presence of these chemicals. Their main purpose is to bind dissimilar materials together, which makes dismantling consumer goods for recycling applications very difficult. In response to prevailing environmental regulations, there is a growing societal effort to reduce our reliance on organic solvents and to develop zero-waste industrial systems.
Glues are typically chemicals that harden when cured. The glue grips mechanically (and sometimes it reacts chemically) with the surfaces being coated as it hardens, forming a continuous and strong layer. Separating the two components requires breaking chemical bonds in the glue, which are often stronger than the components that were joined, resulting in fractures away from the joint.
Sticking materials together with glue is often seen as a permanent solution, and reversing this is a challenge.
From an environmental perspective, water-based glues are becoming more common. “School glues” are based on poly(vinyl acetate), and form a cheap and relatively safe adhesive. Unfortunately, water-based glues soften and degrade in water, although some are better than others. This means that humid environments should be avoided when using water-based glues.
Researching pH-switchable adhesion
In 2007, Professor Mark Geoghegan, then at the University of Sheffield, and his team, showed that if a film of a polycation (a polymer or long chain molecule containing positive charges) came into contact with a polyanion (a negatively charged polymer) gel, they would stick together.
While this result was unsurprising, the team also established that immersion of the bond in either acidic or alkaline media would lead to its failure, causing the two components to separate. This is because at high pH (alkaline), the polycation loses its charge and the same happens at low pH (acid) for the polyanion. The polymers undergo a shape transition when they become neutral; when charged they are extended because the charges on the polymer repel each other, and when uncharged the chains collapse into a coil conformation.
From a thermodynamic perspective, the interaction involves a competition between entropy, elasticity, and electrostatic energy. At high and low pH, only one component is charged, leading to the absence of electrostatic attraction between the components and subsequent bond failure.
Published in 2007, this study primarily served as a proof of principle – it was blue sky research. An actual glue that could be produced easily and stored before use was unavailable. To join surfaces, the end-user had to be prepared to do serious chemistry, which prevented applications of the technology.
Initiating glue innovation: collaboration, expertise and funding
In 2020, Prof. Geoghegan began to explore the feasibility of creating a glue using a process similar to that of creating paint. He hadn’t made a polymer before, despite his significant experience as a polymer scientist. As a physicist interested in the nanoscale, his experience of scale-up and industrial processes was also limited. Seeking assistance, he approached Dr Katarina Novakovic, a chemical engineer with expertise in recycling and valuable industry connections. Together, they secured funding from the Engineering and Physical Sciences Research Council (EPSRC) and hired Dr Adriana Sierra-Romero, a skilled polymer chemist, in 2021 to complete the team.
Making a reversible glue
Dr Sierra-Romero was assigned the task of making a reversible glue, successfully doing so in just four months. Using emulsion polymerization, Dr Sierra-Romero created nanoparticles based on styrene and butyl acrylate in water. The nanoparticles were hydrophobic - meaning they fall out of water - so they needed to be stabilized with a soap. Dr Sierra-Romero used chitosan - a sugar that is positively charged in slightly acidic water - as this stuck very well to the nanoparticles. which gave the team their polycationic emulsion. The anion required using a standard detergent to stabilize the nanoparticles before polymerizing acrylic acid from them, which gave them their polyanion.
Polystyrene is very brittle and poly(butyl acrylate) is very soft. If styrene and butyl acrylate are polymerized together in the right amounts, they can create nanoparticles with the right film-forming properties that are soft enough to coat the surface, and hard enough to provide a stable coating. These formulations were able to coat many plastic surfaces. The team found that when the coated surfaces came into contact, the opposite charges on each formulation attracted, forming a good bond. The bond was not as strong as an epoxy glue but was good enough for many applications and is more effective than sticky tape, for example.
When the joined surfaces were immersed in an acid (pH 2 or lower, which is similar to lemon juice) or in an alkaline medium (pH 12 or higher, which is similar to soapy water), the bond eventually failed. This separates the two components that were previously bonded together and allows them to be recycled.
Effective adhesion on challenging surfaces
Shiny flat plastic surfaces are not suitable for many glues, as they are often unable to get into the microscopic nooks and crannies of the surface and “grip” them. However, the glue our team developed works very well on challenging surfaces.
Polypropylene and low-density polyethylene are plastic packaging materials that Dr Sierra-Romero was able to successfully bond using the glue. Unlike a harsh cyanoacrylate-based superglue alternative, our glue not only unites the surfaces but preserves the flexibility of the plastic. Our adhesive also has the advantage of being relatively transparent.
Our glue is also inherently stable. From time to time, Dr Sierra-Romero would pull an old sample off the shelf and measure the size of the nanoparticles in the formulations. The particles did not change much in size after a whole year, which indicates that the formulations are stable under standard storage conditions.
Improving industrial processes
The team applied for a patent and started talking to industrial partners. Dr Novakovic has contacts in recycling, so the team were able to test the bonding of the adhesive using the wash water at Biffa’s recycling plant at Seaham, County Durham.
Wash water is generally quite alkaline, and the team saw that a polypropylene label would detach from a PET bottle. Labels form about 3% of bottle mass, so recovering these would significantly aid recycling efforts in the bottle recycling industry. The glue is quite safe because it does not contain volatile solvents. This makes it suitable for consumer use. Although we know the glue works, further development is required for consumer applications.
We also get slightly stronger adhesion if we do not use oppositely charged polymers. The polycationic formulation can be used to coat both adhering surfaces and a very good bond is formed, not too far from that of a standard structural adhesive, such as an epoxy. Indeed, for surfaces such as polypropylene, we achieve better adhesion than some structural glues. The downside is that this bond cannot be reversed by washing at high or low pH.
The future: additional funding, extended functionality and team expansion
The EPSRC initially granted two years and £250k to make the glue, but we were invited to try for more funding. We were successful and obtained another £760k and an additional three years. We are now keen to extend the functionality of the glue into new areas, such as recycling in the electronics industry.
Professor Volker Pickert has joined the team as a co-investigator, with his expertise in power electronics. So, an electrical engineer has joined a physicist, chemist, and chemical engineer in this impressive multidisciplinary collaboration. PhD student, Mr Bassam Aljohani (a chemical engineer by training) has already joined to work on formulations for electronics.
Dr Sierra-Romero secured £2.5k and entrepreneurial training, providing invaluable insights into approaching companies and marketing our invention.
It has been quite the journey. What started as blue sky research is now a viable technology that ticks all the boxes for industrial production. The team is now supplementing academic conferences with trade fairs. For the three of us who started, it is very exciting - who knows where this journey will end?
You might also like
- read the paper: Sierra‐Romero, Adriana, et al. “A reversible water-based electrostatic adhesive” Angewandte Chemie International Edition, 2024, 64 e202310750
- find out more in our press release
- meet the team: Dr Adriana Sierra-Romero, Prof Mark Geoghegan and Dr Katarina Novakovic
- read about our School of Engineering and discover our chemical engineering research
- explore the redeveloped Stephenson Building – a beacon for engineering education, research and collaboration
Photo credit: John Donoghue