How our Singapore campus is tackling corrosion with digital twinning
29 April 2024 | By: Newcastle University | 3 min read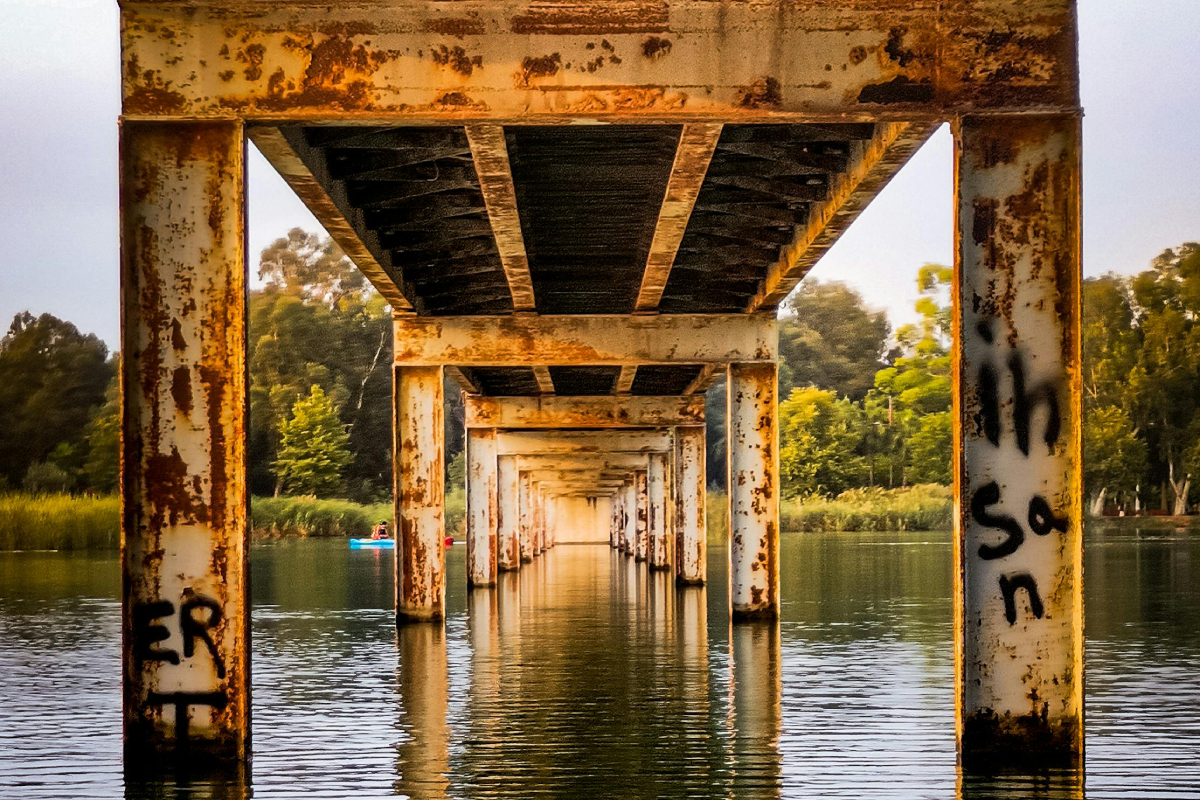
Cathodic protection (CP) is critical in preventing the corrosion of vital infrastructure, such as bridges, pipelines and reinforced concrete structures.
Now, at our Singapore campus, we’re exploring how digital twinning technology can improve the design – and manage the effectiveness – of CP systems.
Contents
- What is cathodic protection
- Why are effective CP systems vital?
- CP systems in Singapore
- Our partnership with Cetim-Matcor
- Digitising CP systems
- Digital twinning in CP systems
- Focusing on accurate corrosion predictions
What is cathodic protection
An electrochemical process, cathodic protection is a way of preventing metal corrosion in wet or underwater environments. Ships, offshore structures such as wind turbines, and even water heaters are all examples of where CP is needed.
CP is achieved by placing anodes around a metal structure. These metal alloy anodes are more easily corroded than the structural material. The anodes draw corrosive energy, a small electrical charge, toward themselves and away from the structure.
Developing systems to deliver CP is complex as they must address several variables. These can range from the nature of a metallic structure to the required life of a system, as well as the temperature, environment and geographic location it’ll be used in.
Why are effective CP systems vital?
Corrosion can have grave implications for numerous industries and jeopardise public safety through structural failures, leaks, and contamination. Substantial economic losses and environmental damage are grave risks if corrosion is not managed.
Overcoming corrosion requires a multidisciplinary approach integrating materials science, electrochemistry, digital technology, and sustainable engineering.
Cathodic protection systems – widely used in civil engineering and the offshore energy industry – can ensure the longevity and integrity of structures, maintaining their reliability while reducing the risks of failures, accidents, environmental damage, and public safety hazards.
CP systems in Singapore
Singapore's economy relies heavily on maritime, offshore energy, and manufacturing industries. As an urbanised and developed nation, its infrastructure – including buildings, bridges, transportation networks, and utility systems – is crucial for maintaining its economy and operations.
Many of those structures, particularly in Singapore's coastal and marine areas, incorporate steel reinforcement or metallic components susceptible to corrosion.
Implementing CP systems can help protect these critical assets from premature degradation, minimise costly repairs or replacements and contribute to the long-term sustainability and resilience of the country’s infrastructure.
Our partnership with Cetim-Matcor
A new PhD project based at Newcastle's Singapore campus is working with Cetim-Matcor, a leading specialist in failure analysis, forensic engineering, materials and corrosion, and asset integrity management. The project aims to improve the accuracy and performance of CP models. It is funded by the Singapore Economic Development Board and Cetim-Matcor.
Cetim, the French Technical Centre for Mechanical Industries, was created in 1965. It provides comprehensive services and solutions to manufacturing industries worldwide, especially aerospace, automotive, energy, and oil and gas.
Together with its international subsidiaries and partners, Cetim serves 8,000 customers in over 50 countries and has become a world-leading engineering group
Matcor is an independent consultancy company in materials and corrosion with over 30 years’ experience. Its core services include failure analysis, forensic engineering investigation, in-situ metallurgical assessment, remnant life assessment, structural and asset integrity assessment, laboratory analysis, advanced NDE, materials performance evaluation, risk-based inspection, and expert witness consultation.
In July 2018, Matcor became Cetim's development platform in Asia Pacific.
Digitising CP systems
The growth of the Industrial Internet of Things (IIoT) and advancements in machine learning have opened up new opportunities for digitising processes such as CP systems through digital twinning.
A digital twin – the virtual representation of an object or system – can represent the real-time condition of a structure and CP system, with live data feeding 3D simulation models. This allows protection levels to be visualised and enable corrective or preventive measures to be taken as needed.
Furthermore, by integrating machine learning, the digital twin can respond proactively to environmental changes such as changes in weather and generate suggestions, or even implement preventive measures, to maintain effective CP.
This intersection of IIoT, digital twins, and machine learning can significantly enhance CP systems’ intelligence, efficiency, and reliability by anticipating and addressing potential challenges, leading to substantial productivity improvements across diverse industries.
Digital twinning in CP systems
Cetim Procor was developed as part of a collaboration between the French Naval Construction Authority (DCNS), the Délégation Générale pour l'Armement (DGA), the French Research Institute for the Exploitation of the Sea (IFREMER), TOTAL, and Cetim.
The software is a robust numerical design and simulation tool for designing the CP of complex installations and structures in humid or marine environments.
A decision support software, it verifies the effectiveness of CP through an interactive process that optimises the positioning of the anodes for the best CP coverage.
In addition, Procor provides information to determine the electromagnetic signature of a structure at sea. By accurately assessing the life of the anodes, it estimates the cost of the various possible CP solutions, considering the installation constraints and maintenance costs, to offer the best technical and economical choice.
Working with Cetim-Matcor we’re aiming to integrate digital twinning and predictive analytics into Procor to address larger projects requiring CP.
The resulting simulations will predict current flow distribution and metal surface potential, optimising CP system designs for maximum protection.
Focusing on accurate corrosion predictions
Incorporating machine learning models for predictive purposes in corrosion-related decisions requires a focus on model interpretability and transparency.
Maintaining Procor's overall robustness, while enhancing its various aspects, poses a key challenge. Therefore, rigorous testing and comprehensive validation are essential to ensure the improved Procor remains dependable for corrosion-related analysis.
The study is comprised of a team of cross-disciplinary specialists:
- Dr Hao Chen; Dr Zi Jie Choong and Dr Jun Jie Chong – assistant professors and the project’s academic supervisors
- Dr Johnathan Tan – R&D engineer and industry supervisor for the project
- Dr Canturri Carla – consultant and industry supervisor for the project
- Prof. Cheng Siong Chin – Chair of Intelligent Systems Modelling and Simulation, who is the academic adviser for the project
The project is progressing successfully, and the team is continually exploring further opportunities for collaborative research projects between Newcastle University in Singapore and Cetim-Matcor.
You might also like:
- Explore our work at Newcastle University in Singapore
- Find out more about Professor Cheng Chin – Chair Professor in Intelligent Systems Modelling and Simulation
- Read more about Cetim-Matcor