From fungi to furniture: the future of sustainable design?
5 March 2024 | By: Newcastle University | 3 min read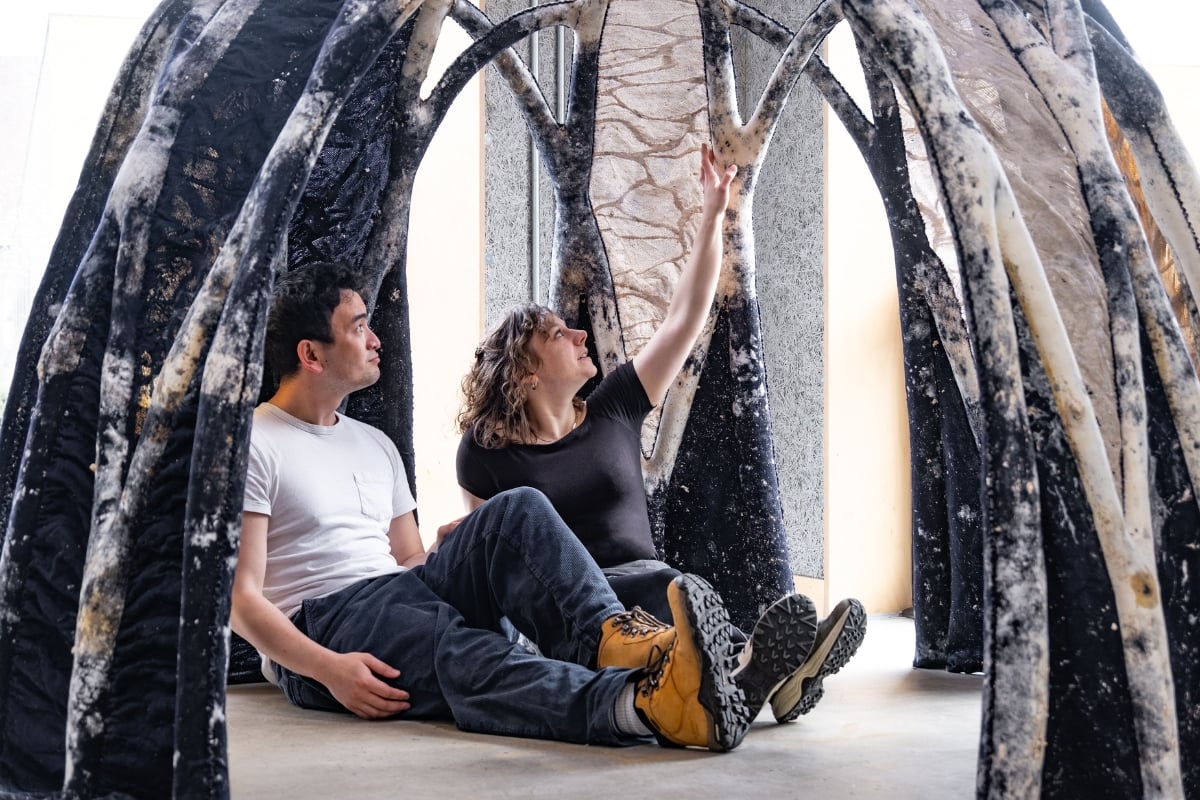
Researchers at the Hub for Biotechnology in the Built Environment have created a material that has huge potential to transform the buildings around us.
Dr Jane Scott is a Newcastle University Academic Track Fellow working at the intersection of programmable materials, knitted fabric design, textile technology and biology.
Jane is part of the multidisciplinary collaborative team that created BioKnit, a unique structure that brings together 3D knitted wool with Mycocrete, made from mycelium, the root network of fungus. The researchers use a knitted wool form to provide the framework for the living material to grow into.
This combination of textiles and mycelium composite offers exciting possibilities. Could we see organically grown buildings in our lifetimes? Or new heat-retaining, fire-resistant, moisture-regulating materials without the use of chemicals?
We spoke to Jane to find out more about her work.
How did you first become interested in the possibilities of mycelium as a material?
Before I joined the Hub for Biotechnology in the Built Environment, I was exploring biomimicry and textiles. I was interested in how nature could inform the kinds of structures and materials I was developing, particularly to produce responsive and smart structures from natural materials. So, there was always a biological focus to my work.
Within the Living Textiles Research Group at Newcastle University, we became really interested in the possibilities of combining mycelium composites with textiles. Particularly, what we could do with textiles that couldn’t be achieved through other systems of forming mycelium composites – using them as a scaffold for growth, and creating new forms not seen before.
The BioKnit team fill mycelium substrate into textile moulds. Credit: Hub for Biotechnology in the Built Environment.
Crucially, we asked ourselves: could this use of textiles be scaled up to make biotech more widespread? A lot of research like this is still at a very small scale because the materials are so new.
But to make an impact on industry and the public, we needed to be able to demonstrate the technology at a building scale. As a structuring system, the use of textiles has allowed us to quickly scale up.
What are some of the biggest challenges you’ve come up against?
The scale up has been a challenge. But we've learned so much by doing it.
Standard prototyping is well understood, but to push this technology into the built environment, we need to understand what happens when we scale these materials up.
We are developing some very unusual approaches to prototyping at scale. We suspend each structure during growth. This means that we can achieve complex curvature as the mycelium grows through the substrate and into the fabric formwork. We have built bespoke growth chambers for each project too, often using conventional scaffolding. The growth chamber provides suitable conditions for mycelium growth, it is important to have a dark environment and maintain heat and moisture levels.
Structure hung in support system. Credit: Ben Bridgens.
But the challenge of scaling up has also brought opportunities. For example, during conventional production, the mycelium is killed with heat. But the structure that we're currently working on, The Growing Room, is three meters high and four meters in diameter, so heat killing it is less straightforward. We dehydrate the structures. The mycelium isn’t going to continue growing, but it's not dead. It can come back to life again.
That’s a really interesting research area. If we can design building materials for circular systems, with an inbuilt second life, that opens up possibilities. We could selectively bring areas of a building back to life. Imagine if you could bio weld a building that needs repair or extension with a join that’s stronger than the original material!
What's next for BioKnit?
We’re not trying to simply replace plasterboard panels with mycelium. We’re trying to enable a different way of building that’s radically more sustainable.
It might require a change in philosophy and a different way of thinking, but there’s huge potential to address urgent sustainability challenges.
That said, the material does have very practical applications that could come through into conventional construction much sooner. We could create interior linings with fantastic insulation properties and improved breathability. It would be a very straightforward way to bring these properties into the interiors of conventional buildings.
Mycelium can transform a loose substrate into a robust composite. This means that we can replace chemical resins and adhesives with products that are better for our health and the environment. It could be transformative for the construction sector.
We are already creating three-metre-high structures, so I’m confident BioKnit has great potential.
The next stage is to start working more closely with industry partners to make sure what we’re doing will be relevant to them – helping them solve challenges and meet regulations. I’d love to hear from anyone interested in exploring practical applications for the material.
You might also like
- you can see The Growing Room on display at Edinburgh Science Festival, 30th March - 14th April 2024 and BioKnit Arch at the London Design Museum until the end of August 2024
- learn more about the BioKnit team, which includes Dr Jane Scott, Romy Kaiser, Armand Agraviador, Prof. Ben Bridgens, Dilan Ozkan and Oliver Perry
- listen to Jane on the From Newcastle podcast: From fungi to Furniture: the future of sustainable design
- explore the Hub for Biotechnology in the Built Environment, and the Living Textiles Research Group
- follow the Hub for Biotechnology in the Built Environment on LinkedIn and Twitter